Virtual Reality, Real Safety

Home Carrie Parashar Jennifer Lastra’s Mission to Save Lives Lorem ipsum dolor sit amet, consectetur adipiscing elit. Ut elit tellus, luctus nec ullamcorper mattis, pulvinar dapibus leo. March 24, 2025 By admin “Compliance doesn’t equal competence. We have to do better.” Jennifer Lastra started her career as an electrician in the US Navy. She spent years working in shipbuilding and manufacturing as boots on the ground. She was welding in shipyards, running electrical lines in high-risk environments. This was real work, alongside people who did dangerous jobs every day. Then she saw the gaps—massive gaps in how safety was taught, understood, and retained. “I didn’t even realize how unsafe shipboard construction was until years later. You’re working with electricity on water. And yet, we weren’t taught about self-awareness or situational awareness the way we should have been. We were just thrown in.” Jennifer Lastra Today, Lastra is on a mission to change that. As the CEO of 360 Immersive, she’s pioneering the use of virtual reality (VR) in safety training. Her firm creates deeply immersive experiences. This is training that forces workers to engage, react, and remember. Her philosophy is simple: traditional training isn’t working. And if the fatality rates prove anything, it’s that the industry is long overdue for disruption. Key Takeaways Lorem Ipsum is simply dummy text of the printing and typesetting industry. Lorem Ipsum has been the industry’s standard dummy text ever since the 1500s, when an unknown printer took a galley of type and scrambled it to make a type specimen book. It has survived not only five centuries, but also Lorem Ipsum is simply dummy text of the printing and typesetting industry. Lorem Ipsum has been the industry’s standard dummy text ever since the 1500s, when an unknown printer took a galley of type and scrambled it to make a type specimen book. It has survived not only five centuries, but also Lorem Ipsum is simply dummy text of the printing and typesetting industry. Lorem Ipsum has been the industry’s standard dummy text ever since the 1500s, when an unknown printer took a galley of type and scrambled it to make a type specimen book. It has survived not only five centuries, but also Lorem Ipsum is simply dummy text of the printing and typesetting industry. Lorem Ipsum has been the industry’s standard dummy text ever since the 1500s, when an unknown printer took a galley of type and scrambled it to make a type specimen book. It has survived not only five centuries, but also From the Navy to Night Vision to VR After the Navy, Lastra moved into shipbuilding. After that — manufacturing, making night vision goggles for military and emergency responders. She loved the sense of service—helping those who protect others. But eventually, she felt the pull to do something on her own. She wanted to build something. And in 2012, she saw her opportunity: virtual reality. “We started being able to pair cell phones with VR viewers,” she says. “Even if it was just cardboard headsets, I knew this technology had the power to completely immerse someone. And if you can immerse them, you can change their behavior.” Jennifer Lastra But Lastra isn’t a tech person. She never set out to be one. What drew her in wasn’t the hardware—it was the potential. “It was the perfect storm,” she says. “Entrepreneurship, powerful technology, and the chance to fix something I knew was broken.” She took that vision and started building. At first, there were skeptics. Some dismissed VR as a gimmick, a novelty. But as more companies saw the results, they realized she was onto something. “When workers go through VR training, they retain more. They react faster. They make better decisions under pressure,” she says. “It’s not theory—it’s science.” Related read: Do you own a business in the insurance industry? Check out how Artificial Intelligence is transforming the insurance industry. Fixing the Gaps in Safety Training For Lastra, the problem with traditional safety training is that it’s passive. Workers sit through hours of slide decks, printed manuals, and video lectures. They check a box, take a test, and move on. But does any of it stick? “Most safety training today is outdated and ineffective,” she says. “We’re giving workers information, but we’re not engaging them. And when the moment comes—when they’re in a real situation—what do they actually remember?” She saw the problem firsthand in her early career. She was dyslexic, struggling to translate technical training into real-world action. “I could pass any test you threw at me,” she says. “But when I got to the fleet, I had no idea how to apply it.” That disconnect drives her work today. 360 Immersive doesn’t just build training programs—it builds experiences. Using VR, workers are placed in hazardous environments. They react, make decisions, and see the consequences of those decisions play out in real time. “The goal is to meet learners where they are,” she says. “Some people learn by reading, some by doing. VR lets us close that gap. It creates a scenario they’ll never forget.” And it’s not just about skill development. VR can replicate real-life pressures. Confined spaces, operating machinery under stress, reacting to an unexpected hazard. “Training should be as close to reality as possible,” Lastra says. “That’s how people learn. That’s how we save lives.” The Next Big Fight: Psychological Safety For Lastra, fixing safety training isn’t just about hazards and compliance—it’s about mindset. She believes the most overlooked factor in workplace safety is psychological safety. “I spent my early career being the only woman on my ship,” she says. “I didn’t feel safe enough to raise my hand and ask a question, even when I didn’t understand something. How many people are in that same position today?” She argues that fear stops workers from speaking up about unsafe conditions. Fear of looking stupid. Fear of retaliation. Fear of being ignored. “People don’t report hazards if they don’t feel like they belong. If they don’t
Top 10 Red Flags in Safety Audits
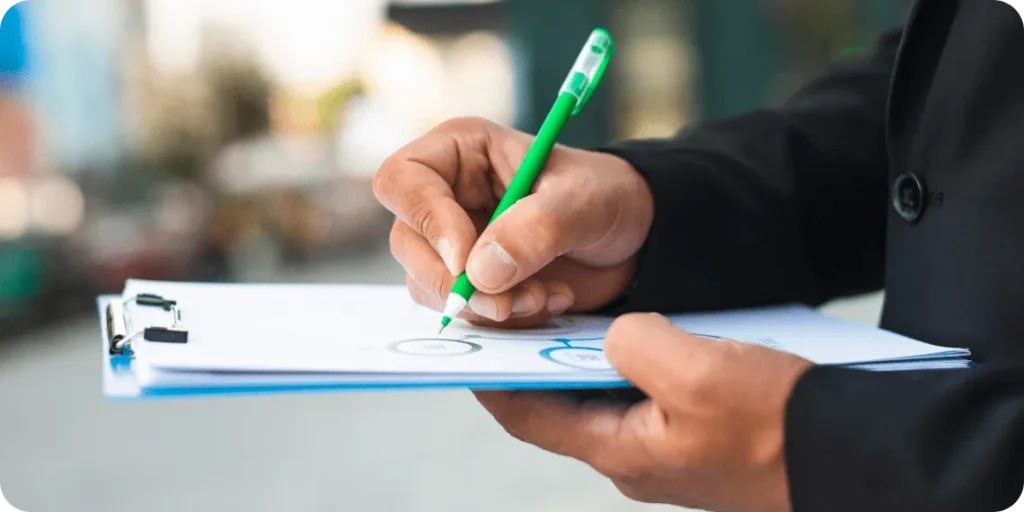
Home Top 10 Red Flags in Safety Audits How to Avoid Them Lorem ipsum dolor sit amet, consectetur adipiscing elit. Ut elit tellus, luctus nec ullamcorper mattis, pulvinar dapibus leo. March 13, 2025 By Dinesh Kumar Safety audits are essential for ensuring workplace compliance and protecting employees. They bring to light the weak points in a safety program and provide actionable insights for improvement. However, common issues can derail audits, leading to penalties, operational disruptions, or worse—preventable incidents. Avoiding these pitfalls doesn’t require perfection. It requires preparation, follow-through, and attention to detail. Here are ten common red flags auditors encounter and practical ways to address them. 1. Disorganized or Missing Documentation The Issue: Incident reports, inspection logs, or training records are incomplete, outdated, or hard to locate. Why It Matters: Documentation is the backbone of safety compliance. Gaps in records raise questions about whether processes are being followed consistently. How to Address It: Store all safety-related documents in a centralized system, whether digital or physical. Automate reminders for updates to keep records current and ensure they’re easily accessible during an audit. 2. Training Records That Don’t Measure Up The Issue: Employees have incomplete or outdated safety training records, including missed refresher courses. Why It Matters: Training equips workers with the knowledge to manage risks effectively. Inadequate records suggest that critical skills and safety protocols may not be properly reinforced. How to Address It: Use a Learning Management System (LMS) to track training participation and completion. Schedule refresher courses at regular intervals and focus on high-risk roles to ensure readiness across the workforce. Key Takeaways Lorem Ipsum is simply dummy text of the printing and typesetting industry. Lorem Ipsum has been the industry’s standard dummy text ever since the 1500s, when an unknown printer took a galley of type and scrambled it to make a type specimen book. It has survived not only five centuries, but also Lorem Ipsum is simply dummy text of the printing and typesetting industry. Lorem Ipsum has been the industry’s standard dummy text ever since the 1500s, when an unknown printer took a galley of type and scrambled it to make a type specimen book. It has survived not only five centuries, but also Lorem Ipsum is simply dummy text of the printing and typesetting industry. Lorem Ipsum has been the industry’s standard dummy text ever since the 1500s, when an unknown printer took a galley of type and scrambled it to make a type specimen book. It has survived not only five centuries, but also Lorem Ipsum is simply dummy text of the printing and typesetting industry. Lorem Ipsum has been the industry’s standard dummy text ever since the 1500s, when an unknown printer took a galley of type and scrambled it to make a type specimen book. It has survived not only five centuries, but also 3. Incomplete Equipment Maintenance Logs The Issue: Maintenance records for machinery or equipment are inconsistent or nonexistent. Why It Matters: Poorly maintained equipment increases the likelihood of accidents and signals a lack of proactive risk management. How to Address It: Implement a maintenance tracking system to log inspections and repairs. Set up automated reminders for routine checks to prevent lapses and ensure that every piece of equipment is safe to operate. 4. Lack of Reporting for Near-Misses The Issue: Near-miss incidents are rarely reported or poorly documented. Why It Matters: Near-misses provide a critical opportunity to address hazards before they escalate into injuries. A lack of reporting indicates potential blind spotsin risk identification. How to Address It: Create a non-punitive reporting system that makes it easy for employees to flag near-misses. Mobile tools or simple forms can streamline the process and encourage participation. 5. PPE Non-Compliance The Issue: Employees are either not wearing or improperly using personal protective equipment (PPE). Why It Matters: Consistent PPE usage is fundamental to workplace safety. Visible lapses undermine compliance efforts and put workers at unnecessary risk. How to Address It: Conduct regular safety observations to verify PPE use and reinforce training on proper practices. Signage in high-risk areas can also serve as a visual reminder. 6. Emergency Plans That Are Outdated or Unpracticed The Issue: Emergency response plans are outdated, incomplete, or haven’t been tested with drills. Why It Matters: An unclear or untested plan can lead to confusion during emergencies, putting workers and operations at greater risk. How to Address It: Review and update emergency plans annually. Conduct drills to test preparedness and ensure employees understand their roles and responsibilities during a crisis. 7. Hazards That Keep Reappearing The Issue: Recurring issues identified in previous audits remain unresolved. Why It Matters: Repeated hazards suggest a lack of accountability and undermine trust in the safety program. How to Address It: Treat audit findings as action items with clear deadlines and responsibilities. Regularly track progress to ensure corrective actions are completed and prevent recurring issues. Related read: Do you own a business in the insurance industry? Check out how Artificial Intelligence is transforming the insurance industry. 8. Disengaged Leadership The Issue: Managers and leadership are absent from safety initiatives or minimally involved in audits. Why It Matters: Leadership involvement is critical for reinforcing a culture of safety. A lack of engagement sends a message that safety isn’t a priority. How to Address It: Involve leaders in safety meetings, audits, and training sessions. Make safety metrics a regular part of leadership reviews to keep it on the agenda and emphasize its importance. 9. Poor Communication of Safety Updates The Issue: Safety updates, protocols, or audit findings aren’t consistently shared with employees. Why It Matters: Gaps in communication lead to confusion, reduced compliance, and repeated issues that could have been avoided with better transparency. How to Address It: Develop a clear communication strategy for all safety updates. Use multiple channels like email, team meetings, and digital dashboards to ensure every employee stays informed. Safety software can track acknowledgment to verify employees receive critical information. 10. Neglected Audit Follow-Ups The Issue: Recommendations from previous audits
Building a Strong Safety Culture
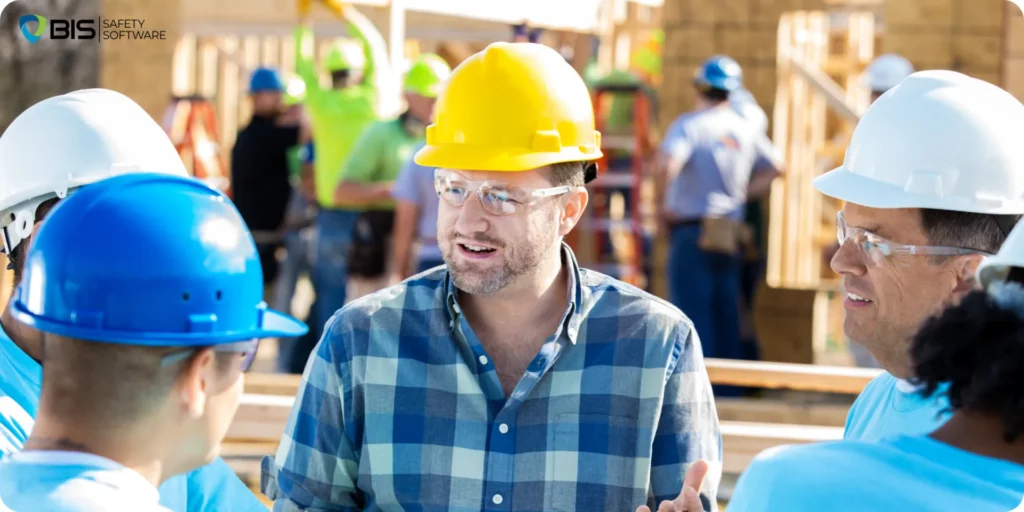
Home Building a Strong Safety Culture 10 Practical Strategies Lorem ipsum dolor sit amet, consectetur adipiscing elit. Ut elit tellus, luctus nec ullamcorper mattis, pulvinar dapibus leo. February 28, 2025 By Divyanshu Jain Creating a strong safety culture takes effort, but the rewards—fewer injuries, lower costs, and a more engaged workforce—are well worth it. Organizations that successfully build a culture of safety don’t just reduce accidents; they improve morale, efficiency, and even profitability. Here are ten essential strategies to strengthen workplace safety: 1. Be Willing to Make Sacrifices Transforming a weak safety culture into a strong one isn’t always easy. It requires hard decisions and, in some cases, a willingness to part ways with employees who refuse to comply. Ted Lane, an Occupational Health and Safety Officer, recalls a major Alberta construction company that implemented a zero-tolerance safety policy. Initially, they lost workers who resisted the new approach, but within a few years, they rebuilt with employees who valued safety. The result? A safer, more efficient, and ultimately more profitable company. 2. Engage Employees in Safety Decisions Many safety policies fail because they are imposed without input from the employees they affect. Workers on the frontlines know the risks better than anyone else, so including them in safety discussions leads to more practical, effective solutions. “We promote the guys to do some of the things in their own way,” says Darryl Chipman, Director for CASCA. “Recently, a worker suggested using pictures instead of a long written form for safety reports. It made things easier, faster, and more effective.” 3. Encourage Candor and Open Communication Employees need to feel safe speaking up about unsafe conditions or behaviors. In organizations with strong safety cultures, workers are encouraged—not punished— for raising concerns. Ted Lane has a unique way of testing this: “I’ll walk into a site missing a piece of safety gear. If a worker stops me and says, ‘Hey, get that fixed,’ I know that company’s culture is working.” Key Takeaways Lorem Ipsum is simply dummy text of the printing and typesetting industry. Lorem Ipsum has been the industry’s standard dummy text ever since the 1500s, when an unknown printer took a galley of type and scrambled it to make a type specimen book. It has survived not only five centuries, but also Lorem Ipsum is simply dummy text of the printing and typesetting industry. Lorem Ipsum has been the industry’s standard dummy text ever since the 1500s, when an unknown printer took a galley of type and scrambled it to make a type specimen book. It has survived not only five centuries, but also Lorem Ipsum is simply dummy text of the printing and typesetting industry. Lorem Ipsum has been the industry’s standard dummy text ever since the 1500s, when an unknown printer took a galley of type and scrambled it to make a type specimen book. It has survived not only five centuries, but also Lorem Ipsum is simply dummy text of the printing and typesetting industry. Lorem Ipsum has been the industry’s standard dummy text ever since the 1500s, when an unknown printer took a galley of type and scrambled it to make a type specimen book. It has survived not only five centuries, but also 4. Lead by Example Leadership must consistently demonstrate their commitment to safety. When managers follow safety protocols, employees are far more likely to do the same. Patrick Cantner, HSE Director of Willbros Canada, advises, “If you say safety comes first, but then reward employees who cut corners to meet deadlines, your safety culture will collapse.” 5. Promote Transparency An open approach to safety builds trust and accountability. Some companies publicly share their safety records and improvement efforts to reinforce the importance of workplace safety. Kinder Morgan sets a high standard by posting safety reports—including injury rates and incidents—on its public website. This level of transparency keeps employees and leadership accountable. 6. Empower Employees to Act Workers must feel confident in stopping unsafe work without fear of retaliation. When employees know they have the authority to halt operations for safety concerns, they become active participants in maintaining a secure workplace. “Our control center operators don’t need approval to shut down a pipeline if they feel there’s an unsafe condition,” says Dan Carter, Director of the Central Region & Control Centre for Kinder Morgan. “That’s built into our procedures.” 7. Make Safety Personal People are more likely to follow safety procedures if they understand the personal impact. Sharon Cole, OHS Consultant for Alberta Gaming and Liquor Corporation, changed a skeptical worker’s attitude by asking him to imagine how he’d feel if his best friend got hurt on the job because he didn’t speak up. That moment of personal connection turned him into one of the most safety-conscious employees on the site. Related read: Do you own a business in the insurance industry? Check out how Artificial Intelligence is transforming the insurance industry. 8. Keep Safety Communication Frequent Safety isn’t a one-time conversation—it’s an ongoing discussion. Monthly safety updates, toolbox talks, and bulletin boards help reinforce key messages. Adam Czarnecki, Human Resource Manager for Great West Kenworth, recommends using statistics to keep employees engaged: “Send out reports on injury trends. Show workers the progress being made.” 9. Recognize and Reward Safe Behavior Positive reinforcement plays a critical role in fostering safety. However, rewards should focus on long-term commitment rather than quick incentives that might encourage underreporting of incidents. Chipman explains, “We offer training and career advancement to employees who prioritize safety. When new safety positions open, we promote from within.” 10. Start With Yourself Safety culture begins with individuals taking personal responsibility. It’s easy to point fingers at management or coworkers, but real change starts when every employee commits to prioritizing safety in their own work. The Real Bottom Line When safety is embedded in an organization’s culture, it doesn’t just prevent accidents—it improves efficiency, morale, and trust. Strong safety cultures don’t develop overnight, but with commitment, consistency, and leadership, they become an essential part
NRCA
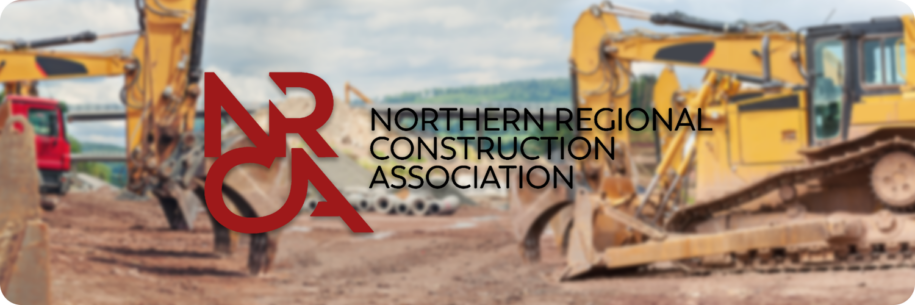
Home NRCA A BIS Authorized Partner Lorem ipsum dolor sit amet, consectetur adipiscing elit. Ut elit tellus, luctus nec ullamcorper mattis, pulvinar dapibus leo. February 26, 2025 By Luca Shillabeer The Northern Regional Construction Association (NRCA) is an industrial, commercial, and institutional sector association serving 120 members across northern British Columbia. As a key advocate for the construction industry in the region, NRCA provides education, training, and support to ensure that its members can build safer and more efficiently. One of NRCA’s primary pillars is education, which is why the association has prioritized partnerships with organizations like BIS Safety Software. ————————————————————————— “One of our big pillars is education, and partnering with BIS allows us to provide members with safety courses that are accessible when they need them.” Kayla Hearn Manager, Operations and Communications ————————————————————————— Strengthening Safety & Industry Growth Founded in the 1960s, NRCA originally served as a community hub, providing plan rooms where members could review construction documents. Over time, the association’s role evolved significantly to include: Education and Training – Offering a range of construction safety courses to meet industry demands. Community Building – Strengthening professional connections and fostering collaboration among members. Advocacy and Support – Ensuring that northern BC’s construction industry has a voice at the provincial level. As the construction landscape changes, NRCA remains committed to adapting alongside its members, helping them stay ahead of industry requirements and best practices. ————————————————————————— ““One of our original purposes was to act as a community hub, and while we still do that, we’ve evolved to focus on educating the community and keeping them building together.“ Kayla Hearn Manager, Operations and Communications ————————————————————————— NRCA is dedicated to uplifting its members and helping them build better. The association operates with a strong regional focus, uniquely serving the needs of construction professionals across northern British Columbia’s vast landscape. Unlike other construction associations in BC, NRCA covers the largest geographical region while being the smallest in membership size. This distinction allows NRCA to provide highly tailored support to its members, ensuring that they receive the resources and training necessary to navigate the specific challenges of northern construction projects. ————————————————————————— “The North is a really specific community on its own, and navigating the challenges that come with that is what sets us apart from other associations across the province” Kayla Hearn Manager, Operations and Communications ————————————————————————— Primary List Of Services Safety Training & Education Industry Advocacy & Support Community Building & Networking Regional Construction Resources Proud To Partner With The NRCA The partnership between the NRCA and BIS Safety Software underscores a shared dedication to workplace safety, education, and industry advancement. By leveraging NRCA’s deep-rooted commitment to supporting construction professionals in northern British Columbia with BIS’s innovative digital training solutions, they are ensuring that workers across remote and urban job sites have seamless access to critical safety education. Together, NRCA and BIS are empowering members with the tools they need to maintain compliance, enhance job site safety, and build a stronger, more resilient workforce. Key Takeaways Lorem Ipsum is simply dummy text of the printing and typesetting industry. Lorem Ipsum has been the industry’s standard dummy text ever since the 1500s, when an unknown printer took a galley of type and scrambled it to make a type specimen book. It has survived not only five centuries, but also Lorem Ipsum is simply dummy text of the printing and typesetting industry. Lorem Ipsum has been the industry’s standard dummy text ever since the 1500s, when an unknown printer took a galley of type and scrambled it to make a type specimen book. It has survived not only five centuries, but also Lorem Ipsum is simply dummy text of the printing and typesetting industry. Lorem Ipsum has been the industry’s standard dummy text ever since the 1500s, when an unknown printer took a galley of type and scrambled it to make a type specimen book. It has survived not only five centuries, but also Lorem Ipsum is simply dummy text of the printing and typesetting industry. Lorem Ipsum has been the industry’s standard dummy text ever since the 1500s, when an unknown printer took a galley of type and scrambled it to make a type specimen book. It has survived not only five centuries, but also Partnership With BIS Safety Software The NRCA has partnered with BIS Safety Software to expand its safety training offerings, making courses more accessible to its members, whether they are working in a city or on a remote job site. The NRCA has significantly expanded its use of BIS’s platform over the past year and plans to continue leveraging its features. ————————————————————————— “We love the service, and we want to keep going ahead with it. It’s something our members can access whether they’re in town or working on a job site,”” Kayla Hearn Manager, Operations and Communications ————————————————————————— Accessibility is a key priority for NRCA, and BIS Safety Software provides an efficient, flexible learning solution that allows members to complete their required safety training on their own schedule. Related read: Do you own a business in the insurance industry? Check out how Artificial Intelligence is transforming the insurance industry. More About The NRCA Serving Northern BC’s Construction Industry The Northern Regional Construction Association (NRCA) supports 120+ members across northern British Columbia, covering the largest geographic region of any construction association in the province. As a dedicated industry advocate, NRCA provides resources, training, and networking opportunities to help members navigate the unique challenges of working in remote and urban construction projects. Committed to Safety & Education Safety training is a core pillar of NRCA, ensuring that construction professionals have access to essential courses that meet industry standards. Through its partnership with BIS Safety Software, NRCA delivers flexible learning solutions, making it easier for workers to stay certified, compliant, and up to date with evolving safety regulations. Strong Community & Industry Advocacy NRCA is more than just a membership association—it is a strong advocate for northern BC’s construction professionals. The organization works closely
Safety Buzz Campus
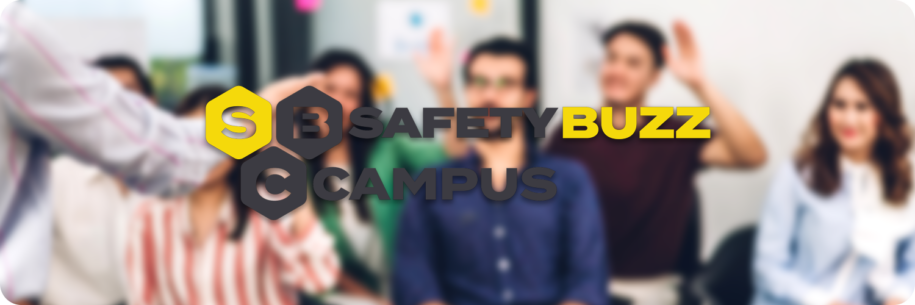
Home Safety Buzz Campus A BIS Authorized Partner Lorem ipsum dolor sit amet, consectetur adipiscing elit. Ut elit tellus, luctus nec ullamcorper mattis, pulvinar dapibus leo. February 25, 2025 By Luca Shillabeer Safety Buzz Campus, based in Dunmore, Alberta, just outside Medicine Hat, has been a cornerstone of safety education and training for over 20 years. Initially focused on delivering core safety courses, the organization has grown into a multifaceted safety training campus with four distinct departments: Safety Training – Offering in-person, online, and off-site safety courses for various industries. Driver Training School – Providing Class 1 and Class 3 driver training programs as part of their comprehensive campus offerings. Safety Management Services – Developing and maintaining customized safety programs for companies to ensure compliance and foster a safety-first culture. Field Safety Services – Supporting off-site safety needs, including confined space monitoring, safety supervision, and equipment such as air trailers and supplied air systems. This comprehensive approach ensures Safety Buzz Campus meets the diverse safety needs of its clients, whether through education, compliance, or on-the-ground support. Tailored Training Solutions The heart of Safety Buzz Campus lies in safety training. From its inception, the organization has been dedicated to building safety cultures within businesses and communities. Their approach goes beyond merely teaching safety practices—they aim to instill an understanding of the purpose and value behind these practices. This commitment helps clients integrate safety into their workplace culture and personal lives. ————————————————————————— “Bringing a safety culture to companies has always been incredibly important. We don’t just like to teach safety practices, we also like to help people understand the value and purpose of it.” Pamela Kunz Safety Buzz Campus Primary List of Services In-house Fall Protection Training Equipment-Specific Courses Safety Training Driver Training School Safety Management Services Field Safety Services Key Takeaways Lorem Ipsum is simply dummy text of the printing and typesetting industry. Lorem Ipsum has been the industry’s standard dummy text ever since the 1500s, when an unknown printer took a galley of type and scrambled it to make a type specimen book. It has survived not only five centuries, but also Lorem Ipsum is simply dummy text of the printing and typesetting industry. Lorem Ipsum has been the industry’s standard dummy text ever since the 1500s, when an unknown printer took a galley of type and scrambled it to make a type specimen book. It has survived not only five centuries, but also Lorem Ipsum is simply dummy text of the printing and typesetting industry. Lorem Ipsum has been the industry’s standard dummy text ever since the 1500s, when an unknown printer took a galley of type and scrambled it to make a type specimen book. It has survived not only five centuries, but also Lorem Ipsum is simply dummy text of the printing and typesetting industry. Lorem Ipsum has been the industry’s standard dummy text ever since the 1500s, when an unknown printer took a galley of type and scrambled it to make a type specimen book. It has survived not only five centuries, but also Proud to Partner with Safety Buzz Campus The partnership between Safety Buzz Campus and BIS Safety Software showcases a shared commitment to advancing safety education across multiple industries. By combining Safety Buzz Campus’s extensive expertise in hands-on training with BIS Safety Software’s innovative digital solutions, they enhance accessibility and efficiency in safety programs. This collaboration streamlines training management, supports compliance, and empowers businesses to cultivate strong safety cultures within their organizations and communities. Partnership with BIS Safety Software Safety Buzz Campus has been leveraging BIS Safety Software for the past five years to streamline their operations. The scheduler feature is a vital tool they use daily to manage training sessions and resources efficiently. ————————————————————————— “We’ve been using BIS for about 5 years now and, clearly it’s designed for the industry. It’s designed exactly the way we need it… The scheduler is the center of our planning and organization.” Pamela Kunz Safety Buzz Campus ————————————————————————— They’re also exploring additional BIS features, such as document creation and CRM capabilities, to maximize the platform’s potential and integrate their diverse services. Looking ahead, they aim to expand their partnership with BIS by digitizing their in-house courses, creating video-based online programs, and enhancing their e-learning offerings. Related read: Do you own a business in the insurance industry? Check out how Artificial Intelligence is transforming the insurance industry. More about Safety Buzz Campus Community Engagement Safety Buzz Campus is deeply rooted in its community. Beyond their training services, the team actively participates in local events, volunteering for organizations like food banks and music festivals to provide on-site first aid and other support. “We’re not just a business; we’re part of the community. From volunteering at the local food bank to supporting music festivals with first aid services, we’re committed to giving back,” Pamela explained. Their connection to the community strengthens their reputation as a trusted partner in safety education and services. Company Culture Safety Buzz Campus prides itself on fostering a team-oriented and employee-centric culture. The owners prioritize creating a supportive environment where team members can thrive. This internal focus on safety and collaboration ensures they practice what they promote to clients. “We focus on building a strong internal safety culture because we can’t promote what we don’t practice. Our team is solid, and we’re excited about our future growth,” Pamela noted. Industries Served While Safety Buzz Campus has deep roots in oil and gas, they’ve expanded their reach to include construction, agriculture, and even unique clients like golf courses and senior living facilities. Recently, they: Revamped the safety program for a local golf course after a compliance inquiry. Provided safety training for staff at a senior living facility during their annual safety day. Partnered with a local school to deliver agricultural safety training to students in Grades 7-9, tailoring lessons to young learners with a focus on farm safety. These initiatives reflect Safety Buzz Campus’s adaptability and commitment to safety education across a diverse range of industries.