Virtual Reality, Real Safety

Home Carrie Parashar Jennifer Lastra’s Mission to Save Lives Lorem ipsum dolor sit amet, consectetur adipiscing elit. Ut elit tellus, luctus nec ullamcorper mattis, pulvinar dapibus leo. March 24, 2025 By admin “Compliance doesn’t equal competence. We have to do better.” Jennifer Lastra started her career as an electrician in the US Navy. She spent years working in shipbuilding and manufacturing as boots on the ground. She was welding in shipyards, running electrical lines in high-risk environments. This was real work, alongside people who did dangerous jobs every day. Then she saw the gaps—massive gaps in how safety was taught, understood, and retained. “I didn’t even realize how unsafe shipboard construction was until years later. You’re working with electricity on water. And yet, we weren’t taught about self-awareness or situational awareness the way we should have been. We were just thrown in.” Jennifer Lastra Today, Lastra is on a mission to change that. As the CEO of 360 Immersive, she’s pioneering the use of virtual reality (VR) in safety training. Her firm creates deeply immersive experiences. This is training that forces workers to engage, react, and remember. Her philosophy is simple: traditional training isn’t working. And if the fatality rates prove anything, it’s that the industry is long overdue for disruption. Key Takeaways Lorem Ipsum is simply dummy text of the printing and typesetting industry. Lorem Ipsum has been the industry’s standard dummy text ever since the 1500s, when an unknown printer took a galley of type and scrambled it to make a type specimen book. It has survived not only five centuries, but also Lorem Ipsum is simply dummy text of the printing and typesetting industry. Lorem Ipsum has been the industry’s standard dummy text ever since the 1500s, when an unknown printer took a galley of type and scrambled it to make a type specimen book. It has survived not only five centuries, but also Lorem Ipsum is simply dummy text of the printing and typesetting industry. Lorem Ipsum has been the industry’s standard dummy text ever since the 1500s, when an unknown printer took a galley of type and scrambled it to make a type specimen book. It has survived not only five centuries, but also Lorem Ipsum is simply dummy text of the printing and typesetting industry. Lorem Ipsum has been the industry’s standard dummy text ever since the 1500s, when an unknown printer took a galley of type and scrambled it to make a type specimen book. It has survived not only five centuries, but also From the Navy to Night Vision to VR After the Navy, Lastra moved into shipbuilding. After that — manufacturing, making night vision goggles for military and emergency responders. She loved the sense of service—helping those who protect others. But eventually, she felt the pull to do something on her own. She wanted to build something. And in 2012, she saw her opportunity: virtual reality. “We started being able to pair cell phones with VR viewers,” she says. “Even if it was just cardboard headsets, I knew this technology had the power to completely immerse someone. And if you can immerse them, you can change their behavior.” Jennifer Lastra But Lastra isn’t a tech person. She never set out to be one. What drew her in wasn’t the hardware—it was the potential. “It was the perfect storm,” she says. “Entrepreneurship, powerful technology, and the chance to fix something I knew was broken.” She took that vision and started building. At first, there were skeptics. Some dismissed VR as a gimmick, a novelty. But as more companies saw the results, they realized she was onto something. “When workers go through VR training, they retain more. They react faster. They make better decisions under pressure,” she says. “It’s not theory—it’s science.” Related read: Do you own a business in the insurance industry? Check out how Artificial Intelligence is transforming the insurance industry. Fixing the Gaps in Safety Training For Lastra, the problem with traditional safety training is that it’s passive. Workers sit through hours of slide decks, printed manuals, and video lectures. They check a box, take a test, and move on. But does any of it stick? “Most safety training today is outdated and ineffective,” she says. “We’re giving workers information, but we’re not engaging them. And when the moment comes—when they’re in a real situation—what do they actually remember?” She saw the problem firsthand in her early career. She was dyslexic, struggling to translate technical training into real-world action. “I could pass any test you threw at me,” she says. “But when I got to the fleet, I had no idea how to apply it.” That disconnect drives her work today. 360 Immersive doesn’t just build training programs—it builds experiences. Using VR, workers are placed in hazardous environments. They react, make decisions, and see the consequences of those decisions play out in real time. “The goal is to meet learners where they are,” she says. “Some people learn by reading, some by doing. VR lets us close that gap. It creates a scenario they’ll never forget.” And it’s not just about skill development. VR can replicate real-life pressures. Confined spaces, operating machinery under stress, reacting to an unexpected hazard. “Training should be as close to reality as possible,” Lastra says. “That’s how people learn. That’s how we save lives.” The Next Big Fight: Psychological Safety For Lastra, fixing safety training isn’t just about hazards and compliance—it’s about mindset. She believes the most overlooked factor in workplace safety is psychological safety. “I spent my early career being the only woman on my ship,” she says. “I didn’t feel safe enough to raise my hand and ask a question, even when I didn’t understand something. How many people are in that same position today?” She argues that fear stops workers from speaking up about unsafe conditions. Fear of looking stupid. Fear of retaliation. Fear of being ignored. “People don’t report hazards if they don’t feel like they belong. If they don’t
Safety Myths
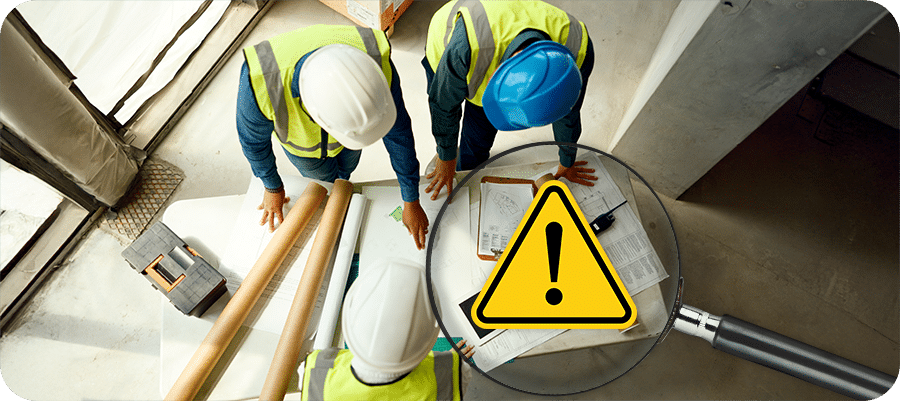
Home Safety Myths That Need to Die Lorem ipsum dolor sit amet, consectetur adipiscing elit. Ut elit tellus, luctus nec ullamcorper mattis, pulvinar dapibus leo. March 14, 2025 By Luke Hillenbrand Some workplace safety “truths” have been passed down for years—but that doesn’t make them right. In fact, some of the most common safety beliefs are flat-out dangerous. It’s time to call them out before they get someone hurt. Here are some of the biggest myths that need to be put to bed: 1. “We’ve Always Done It This Way, and It’s Been Fine” Why it’s dangerous: Just because it worked before doesn’t mean it’s safe now. The fix: Regularly review procedures and update them based on new technology and best practices. Just because something hasn’t caused an accident yet doesn’t mean it won’t. Luck is not a safety strategy. Every shortcut taken without consequence is just stacking the odds against you. The right way to do something is the safe way—not just the way it’s always been done. This myth is especially dangerous because it resists change. New technology, updated regulations, and evolving best practices exist for a reason. Sticking to outdated methods means ignoring safer, more efficient ways to work. It’s only a matter of time before that “tried and true” approach fails in a catastrophic way. ————————————————————————— “People with [differing] attitudes or inexperience think they can cut corners, but it will catch up with them eventually. It’s just like running stop signs—you might get away with it for a while, but sooner or later, disaster strikes.” Robin Postnikoff ————————————————————————— 2. “More PPE Means More Safety” Why it’s dangerous: Too much PPE can reduce mobility and create new hazards. The fix: Use the hierarchy of controls—eliminate hazards first, then rely on PPE as a last line of defense. PPE is essential, but it’s not a magic shield. Wearing thick gloves while handling tiny components can reduce grip and increase risk. Heavy gear in hot conditions can lead to heat exhaustion. Safety starts with eliminating hazards—not just piling on more protective equipment. The key is the hierarchy of controls. Remove the hazard first. Substitute safer alternatives. Install engineering or administrative controls before relying solely on PPE. Workers need the right protection, not just more protection. Key Takeaways Lorem Ipsum is simply dummy text of the printing and typesetting industry. Lorem Ipsum has been the industry’s standard dummy text ever since the 1500s, when an unknown printer took a galley of type and scrambled it to make a type specimen book. It has survived not only five centuries, but also Lorem Ipsum is simply dummy text of the printing and typesetting industry. Lorem Ipsum has been the industry’s standard dummy text ever since the 1500s, when an unknown printer took a galley of type and scrambled it to make a type specimen book. It has survived not only five centuries, but also Lorem Ipsum is simply dummy text of the printing and typesetting industry. Lorem Ipsum has been the industry’s standard dummy text ever since the 1500s, when an unknown printer took a galley of type and scrambled it to make a type specimen book. It has survived not only five centuries, but also Lorem Ipsum is simply dummy text of the printing and typesetting industry. Lorem Ipsum has been the industry’s standard dummy text ever since the 1500s, when an unknown printer took a galley of type and scrambled it to make a type specimen book. It has survived not only five centuries, but also ————————————————————————— “Sometimes, extreme PPE requirements actually cause more problems. We had sites where tying off at two steps was mandatory, but workers were tripping over their harness cords. It wasn’t reasonable, and people got hurt because of it.” Brett Burkard ————————————————————————— 3. “A Quick Task Doesn’t Need Full Safety Precautions” Why it’s dangerous: Accidents happen in seconds, especially when rushing. The fix: Treat every task—no matter how small—as an opportunity to follow proper safety procedures. The worst accidents happen when people skip safety steps “just for a second.” It only takes a moment for a fall, a fire, or an amputation to happen. No job is too small for safety. Related read: Do you own a business in the insurance industry? Check out how Artificial Intelligence is transforming the insurance industry. ————————————————————————— “Every rule has been written in blood. People don’t take things seriously until someone gets hurt or a company gets sued. That’s why we drill safety into training—it has to stick before something bad happens.” Robin Postnikoff ————————————————————————— 4. “If It’s Not an Injury, It’s Not a Big Deal” Why it’s dangerous: Near misses are warnings that something is wrong. The fix: Investigate and correct all near misses before they turn into serious accidents. Near misses are flashing warning signs. Ignoring them guarantees that next time, someone will get hurt. Treat close calls like actual incidents—investigate, correct, and learn from them. In industries like construction and manufacturing, near misses are often precursors to severe accidents. A worker who trips but doesn’t fall today might break a leg tomorrow. A machine that jams without consequence today might lead to an amputation next week. Reporting and addressing near misses prevent tragedies. 5. “Good Workers Don’t Need Safety Training” Why it’s dangerous: Experience can lead to overconfidence and complacency. The fix: Make regular safety training mandatory for all employees, no matter their experience level. Experience doesn’t make anyone invincible. In fact, veteran workers are often the ones who get complacent. Training isn’t just for rookies—it’s for everyone, all the time. ————————————————————————— “I don’t care if you have a master’s degree in safety. If you don’t have the experience, the network, and the mindset to keep learning, you’re not going to be a good safety person. Training is never just a ‘one and done.” Kevin Swinden ————————————————————————— 6. “Slower Work Is Safer Work” Why it’s dangerous: Moving too slowly can cause inefficiencies and increase risk. The fix: Focus on smart work—trained, controlled, and precise—rather than
Would You Bet Your Paycheck on Safety?
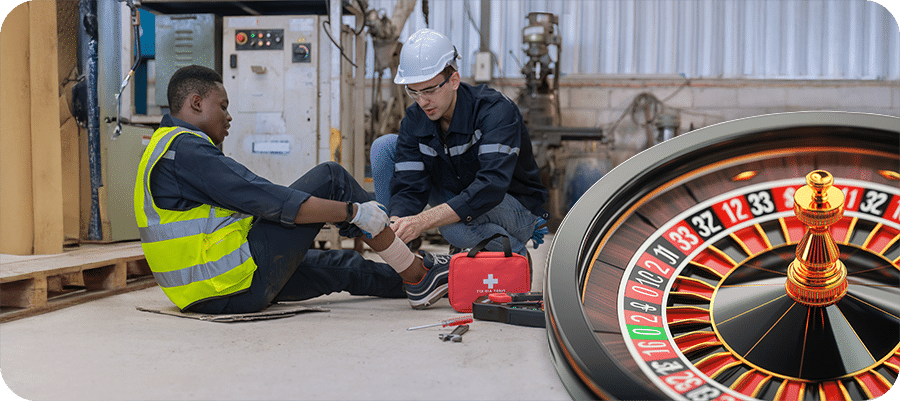
Home Would You Bet Your Paycheck on Safety? That Need to Die Lorem ipsum dolor sit amet, consectetur adipiscing elit. Ut elit tellus, luctus nec ullamcorper mattis, pulvinar dapibus leo. March 14, 2025 By Luke Hillenbrand Imagine this: At the end of every shift, you had to bet your entire paycheck that nobody on your crew got hurt. Would you do anything differently? Would you double-check your PPE? Would you remind a co-worker to use a harness? Would you take that extra second to secure a load or test a machine lockout? The truth is, whether you realize it or not, you are betting on safety every day. The stakes aren’t just money—they’re your health, your reputation, and your future. One bad decision, one shortcut, one ignored hazard, and you could lose everything. Safety is More Than a Rule—It’s a Wager Most people wouldn’t gamble their paycheck on pure luck. But every time someone skips a step, assumes a risk, or rushes a job, they’re rolling the dice. Sometimes they win—nothing happens. Other times? That bet costs them weeks of lost wages, medical bills, or a permanent injury. Think about it: A mechanic skips wearing gloves because “it’s just a quick fix.” That quick fix leads to stitches and time off work. A forklift operator speeds up to finish early. One wrong turn leads to a collision—and unemployment. A roofer skips fall protection “just for a second.” That second changes their life forever. Key Takeaways Lorem Ipsum is simply dummy text of the printing and typesetting industry. Lorem Ipsum has been the industry’s standard dummy text ever since the 1500s, when an unknown printer took a galley of type and scrambled it to make a type specimen book. It has survived not only five centuries, but also Lorem Ipsum is simply dummy text of the printing and typesetting industry. Lorem Ipsum has been the industry’s standard dummy text ever since the 1500s, when an unknown printer took a galley of type and scrambled it to make a type specimen book. It has survived not only five centuries, but also Lorem Ipsum is simply dummy text of the printing and typesetting industry. Lorem Ipsum has been the industry’s standard dummy text ever since the 1500s, when an unknown printer took a galley of type and scrambled it to make a type specimen book. It has survived not only five centuries, but also Lorem Ipsum is simply dummy text of the printing and typesetting industry. Lorem Ipsum has been the industry’s standard dummy text ever since the 1500s, when an unknown printer took a galley of type and scrambled it to make a type specimen book. It has survived not only five centuries, but also The House Always Wins Casinos are designed so that, over time, the house always wins. Unsafe work habits work the same way. Maybe you’ve skipped safety steps before and nothing happened. Maybe you’ve seen others take risks and walk away fine. That’s like winning a few hands in a row—it feels good, but the odds will catch up eventually. Complacency is the biggest con of all. The more times a worker gets away with a risk, the more confident they become in their luck. But luck runs out. And when it does, the price is steep. Related read: Do you own a business in the insurance industry? Check out how Artificial Intelligence is transforming the insurance industry. How to Play It Safe (and Win Every Time) 1. Be Smart Act like your paycheck depends on it. Because in many ways, it does. 2. Think Long-Term A shortcut might save five minutes, but an injury could cost five months. 3. Hold Each Other Accountable Safety isn’t a solo game. Watch out for your crew. Remind them that a mistake could cost them more than just pride. 4. Stay Sharp Keep safety top of mind. Refresh your training. Don’t let routine make you careless. 5. Call Out the Risks If something feels unsafe, stop. Speak up. Fix it before it becomes an accident. Make the Right Bet If you had to bet your paycheck on safety, you’d work smarter. You’d pay attention. You’d make sure nobody around you was cutting corners. You’d take safety seriously—because you’d have too much to lose. The reality? You already do. Every shift, every task, every decision is a bet. Make sure it’s one you can afford to win. Stay sharp. Stay safe. Because in this game, there’s no cashing out. BIS Social Media Follow BIS Safety Software for industry-leading safety updates, training solutions, and more. Hover over each icon for quick access to follow, share, or explore our other channels. Frequently Asked Questions Have question in mind? We are here to answer. If you don’t see your question here, drop us a line at our contact page. Lorem Ipsum is simply dummy text of the printing and typesetting industry? Lorem ipsum dolor sit amet, consectetur adipiscing elit. Ut elit tellus, luctus nec ullamcorper mattis, pulvinar dapibus leo. Lorem Ipsum is simply dummy text of the printing and typesetting industry? Lorem ipsum dolor sit amet, consectetur adipiscing elit. Ut elit tellus, luctus nec ullamcorper mattis, pulvinar dapibus leo. Lorem Ipsum is simply dummy text of the printing and typesetting industry? Lorem ipsum dolor sit amet, consectetur adipiscing elit. Ut elit tellus, luctus nec ullamcorper mattis, pulvinar dapibus leo. Lorem Ipsum is simply dummy text of the printing and typesetting industry? Lorem ipsum dolor sit amet, consectetur adipiscing elit. Ut elit tellus, luctus nec ullamcorper mattis, pulvinar dapibus leo. Lorem Ipsum is simply dummy text of the printing and typesetting industry? Lorem ipsum dolor sit amet, consectetur adipiscing elit. Ut elit tellus, luctus nec ullamcorper mattis, pulvinar dapibus leo. Lorem ipsum dolor sit amet, consectetur adipiscing elit. Ut elit tellus, luctus nec ullamcorper mattis, pulvinar dapibus leo. Lorem ipsum dolor sit amet, consectetur adipiscing elit. Ut elit tellus, luctus nec ullamcorper mattis, pulvinar dapibus leo. Lorem ipsum dolor sit amet, consectetur adipiscing elit. Ut
Safety Meets Tech:

Home Safety Meets Tech: The Evolution of Wearable Safety Devices Lorem ipsum dolor sit amet, consectetur adipiscing elit. Ut elit tellus, luctus nec ullamcorper mattis, pulvinar dapibus leo. March 13, 2025 By Luke Hillenbrand Workplace safety is evolving. Technology is changing the game. Wearable devices are at the forefront, combining tech and practicality. They protect workers, enhance efficiency, and reduce risks. From smart helmets to biometric sensors, these tools are transforming high-risk environments. Companies investing in them build safer, more productive futures, improving both employee welfare and operational success. With each advancement, these devices demonstrate their potential to reshape workplace safety for good. A Brief History of Wearable Safety Devices Wearable safety isn’t new. For decades, workers relied on helmets, gloves, and goggles to stay safe. Technology changed that. Early alarm systems, like vibration alerts in mining helmets, warned of dangers such as collapsing shafts or unstable terrain. These innovations paved the way for today’s advanced devices. With sensors, GPS, and real-time data, modern wearables are more than protective gear—they are integral tools for workplace safety. From alerting workers in hazardous zones to collecting data that informs long-term safety strategies, wearables have come a long way. The journey from basic alerts to predictive analytics highlights a growing commitment to reducing risks and safeguarding lives. Types of Wearable Safety Devices Modern wearables tackle specific hazards with precision and adaptability: Smart Helmets Equipped with AR (augmented reality), these helmets detect gas leaks and structural hazards. They provide instant alerts and facilitate communication on job sites. Some models integrate thermal imaging to detect hidden dangers, such as overheating machinery or fire risks. Enhanced sensors now enable predictive maintenance, flagging potential failures before they occur. Biometric Sensors These devices monitor vital signs like heart rate, hydration, and body temperature. Advanced models analyze stress levels and alert workers before fatigue sets in, preventing accidents caused by exhaustion. Sensors can now integrate with wearable patches that track hydration in real-time, offering on-the-spot health recommendations. Location Trackers GPS-powered trackers locate lone workers and ensure rapid response during emergencies. Geofencing features notify supervisors when workers enter restricted zones, reinforcing site protocols. New multi-network connectivity ensures these trackers remain operational even in remote locations. Exoskeletons Designed to support lifting tasks, exoskeletons reduce strain and prevent musculoskeletal injuries. They enhance physical endurance, allowing workers to perform repetitive tasks safely. Some models are now powered by AI, adapting to users’ movements for optimized support. Smart Glasses AR overlays provide hands-free access to instructions and safety checklists. These glasses improve precision and reduce downtime by streamlining workflows. Advanced glasses include voice control and facial recognition, enabling rapid identification of team members and secure data sharing. Environmental Monitors These devices detect airborne hazards, such as toxic gases or particulates, ensuring real-time protection in industries like mining and chemical manufacturing. Newer versions now combine weather sensors, giving additional insights into changing conditions that could pose risks. Key Takeaways Lorem Ipsum is simply dummy text of the printing and typesetting industry. Lorem Ipsum has been the industry’s standard dummy text ever since the 1500s, when an unknown printer took a galley of type and scrambled it to make a type specimen book. It has survived not only five centuries, but also Lorem Ipsum is simply dummy text of the printing and typesetting industry. Lorem Ipsum has been the industry’s standard dummy text ever since the 1500s, when an unknown printer took a galley of type and scrambled it to make a type specimen book. It has survived not only five centuries, but also Lorem Ipsum is simply dummy text of the printing and typesetting industry. Lorem Ipsum has been the industry’s standard dummy text ever since the 1500s, when an unknown printer took a galley of type and scrambled it to make a type specimen book. It has survived not only five centuries, but also Lorem Ipsum is simply dummy text of the printing and typesetting industry. Lorem Ipsum has been the industry’s standard dummy text ever since the 1500s, when an unknown printer took a galley of type and scrambled it to make a type specimen book. It has survived not only five centuries, but also Industries Leading the Adoption of Wearable Technology Industries with high risks are leading the way in wearable adoption. Their focus on safety and efficiency makes wearables indispensable tools: Construction Smart helmets and trackers improve site safety, aiding navigation through busy or hazardous areas. By providing real-time updates, they reduce the chance of accidents. Wearables also integrate with project management software, enhancing coordination and efficiency. Oil and Gas Biometric sensors and gas detectors protect workers from harmful exposures. Wearables also ensure compliance with safety standards in environments where stakes are high. Some systems now include drone connectivity, combining aerial surveillance with wearable monitoring. Manufacturing Exoskeletons reduce physical strain, while smart glasses streamline precision tasks. These technologies improve productivity while cutting down on workplace injuries. Collaborative robots (cobots) now pair with wearables for seamless workflows. Healthcare Wearables track stress and fatigue during long shifts, protecting healthcare professionals in high-pressure environments. Devices like wearable ECG monitors safeguard their health while improving patient care. Integration with telehealth platforms ensures that real-time data supports decision-making. Mining Monitors and trackers enhance safety in remote and hazardous locations. Advanced systems ensure miners can be located and rescued swiftly in emergencies. Combined with underground communication networks, these tools ensure 24/7 connectivity in challenging conditions. Related read: Do you own a business in the insurance industry? Check out how Artificial Intelligence is transforming the insurance industry. Benefits of Wearable Safety Technology 1. Real-Time Monitoring Continuous data collection allows for instant responses, preventing accidents before they occur. Live dashboards centralize this data, providing supervisors with actionable insights. 2. Enhanced Compliance Automated tracking simplifies adherence to safety protocols, reducing manual errors. Regulatory updates can be pushed directly to wearables, ensuring workers remain informed. 3. Improved Productivity Ergonomic support minimizes injuries and fatigue, boosting worker efficiency. Wearables also streamline workflows, allowing workers to focus on tasks without interruptions. 4.
How to Turn Incident Data
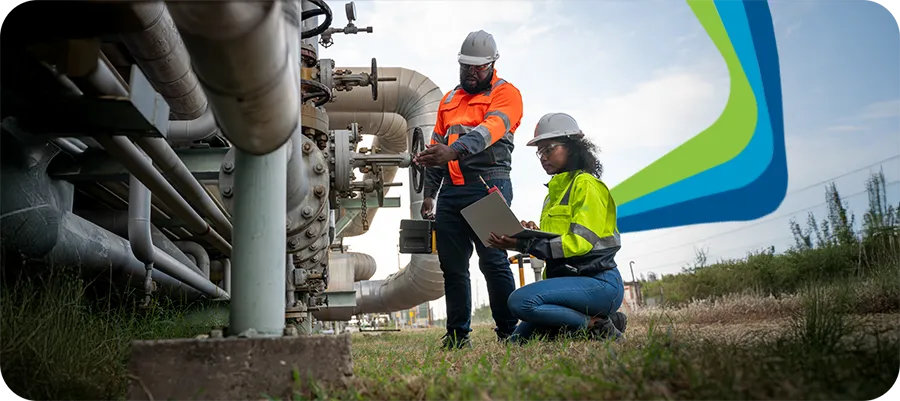
Home How to Turn Incident Data Into Actionable Insights Lorem ipsum dolor sit amet, consectetur adipiscing elit. Ut elit tellus, luctus nec ullamcorper mattis, pulvinar dapibus leo. March 13, 2025 By Luke Hillenbrand Every workplace safety program generates incident data, but not all organizations know how to make the most of it. Incident reports, near-miss logs, and safety observations provide more than just numbers—they reveal patterns, highlight risks, and offer a roadmap for improvement. The challenge lies in translating this raw data into clear, actionable insights that drive meaningful change. Without the right strategies, data can remain an untapped resource, leaving organizations reactive instead of proactive. This guide explores how to analyze incident data effectively, identify trends, and use those insights to enhance workplace safety. Why Incident Data Matters Incident data isn’t just a record of what’s gone wrong—it’s a tool for understanding the “why” behind workplace risks. Every report contains valuable information about hazards, behaviors, and system failures that contribute to incidents. When analyzed effectively, this data helps organizations: Identify Patterns Highlight recurring risks and pinpoint high-risk areas, equipment, or processes. Drive Preventive Measures Use trends to implement targeted safety improvements before incidents escalate. Support Compliance Provide documentation that demonstrates a proactive approach to safety during audits. Boost Accountability Show clear links between safety initiatives and outcomes, reinforcing a culture of responsibility. By leveraging incident data, safety managers can shift from reacting to problems to preventing them entirely. Step 1: Collect Consistent, High-Quality Data The foundation of actionable insights is reliable data. Inconsistent or incomplete incident reporting undermines your ability to draw meaningful conclusions. Best Practices for Data Collection Standardized Reporting Forms Ensure every incident report includes key details such as date, time, location, individuals involved, and a clear description of the event. Encourage Near-Miss Reporting Near-misses are early warning signs of potential hazards. Make it easy and non-punitive for employees to report them. Use Mobile Tools Digital reporting systems streamline data collection and reduce errors compared to paper-based processes. Case Study: A logistics company implemented a mobile app for near-miss reporting. Within six months, reports increased by 40%, uncovering trends related to poorly marked loading zones. Addressing these issues reduced incidents by 25% the following quarter. Step 2: Centralize and Organize Your Data Scattered data creates blind spots. Consolidating all incident reports, safety observations, and inspection logs into a centralized system ensures nothing slips through the cracks. How to Centralize Effectively Use Safety Management Software Platforms designed for workplace safety consolidate data into a single dashboard, making it easy to analyze trends. Tag and Categorize Data Organize reports by type, location, equipment, or contributing factors to identify recurring issues. Integrate With Existing Systems Ensure your safety software connects with HR, maintenance, and compliance platforms to provide a comprehensive view. Pro Tip: Regularly review your data for completeness and consistency. Missing or inaccurate information can skew results and lead to flawed conclusions. Key Takeaways Lorem Ipsum is simply dummy text of the printing and typesetting industry. Lorem Ipsum has been the industry’s standard dummy text ever since the 1500s, when an unknown printer took a galley of type and scrambled it to make a type specimen book. It has survived not only five centuries, but also Lorem Ipsum is simply dummy text of the printing and typesetting industry. Lorem Ipsum has been the industry’s standard dummy text ever since the 1500s, when an unknown printer took a galley of type and scrambled it to make a type specimen book. It has survived not only five centuries, but also Lorem Ipsum is simply dummy text of the printing and typesetting industry. Lorem Ipsum has been the industry’s standard dummy text ever since the 1500s, when an unknown printer took a galley of type and scrambled it to make a type specimen book. It has survived not only five centuries, but also Lorem Ipsum is simply dummy text of the printing and typesetting industry. Lorem Ipsum has been the industry’s standard dummy text ever since the 1500s, when an unknown printer took a galley of type and scrambled it to make a type specimen book. It has survived not only five centuries, but also Step 3: Analyze for Patterns and Trends Once your data is centralized, the next step is to identify patterns that point to underlying risks. Look for clusters of similar incidents or recurring hazards across locations. What to Look For Recurring Equipment Failures Are specific machines or tools involved in multiple incidents? Time-Based Trends Do incidents spike during certain shifts or seasons? Location-Specific Risks Are certain areas of your facility more prone to hazards? Example in Action: A manufacturing plant noticed a pattern of injuries involving workers replacing conveyor belts during peak shifts. The analysis revealed that time pressures led to shortcuts in safety procedures. By scheduling maintenance during slower periods and providing additional training, the company reduced injuries by 30%. Step 4: Translate Insights Into Actionable Changes Data is only as valuable as the actions it inspires. Once trends are identified, use them to implement targeted improvements. Strategies for Acting on Insights Revise Policies Update safety protocols to address identified risks, such as enhanced procedures for high-risk tasks. Targeted Training Provide specific training sessions based on the most common incident types or contributing factors. Engineering Controls Modify equipment, tools, or workspaces to eliminate hazards entirely. Case Study: A construction company analyzed incident reports and found that ladder-related falls were a recurring issue. They introduced new ladder inspection protocols, provided hands-on training, and replaced aging equipment. The result? A 50% decrease in ladder-related injuries within a year. Step 5: Share Insights With Your Team Transparency is key to fostering a safety-first culture. Sharing insights from incident data helps employees understand risks and reinforces their role in creating a safer workplace. How to Communicate Effectively Visual Dashboards Use charts, graphs, and heatmaps to make data easy to understand. Regular Safety Meetings Discuss trends and progress during team huddles or monthly safety reviews. Highlight Successes Celebrate reductions in incidents
Shortcuts Kill

Home Shortcuts Kill The Hidden Cost of Rushing Through Safety Lorem ipsum dolor sit amet, consectetur adipiscing elit. Ut elit tellus, luctus nec ullamcorper mattis, pulvinar dapibus leo. March 7, 2025 By Luke Hillenbrand Shortcuts save time—until they don’t. A missing hard hat. A skipped lockout. A harness left unclipped. One bad decision can change everything. Workers take risks when they think nothing will go wrong. Until it does. And when it does, it’s fast. Sudden. Unforgiving. One moment of carelessness can lead to an injury, a shutdown, or a life-changing disaster. The Danger of Cutting Corners Rushing feels efficient. Deadlines press. Supervisors push for speed. But cutting corners doesn’t just shave minutes—it adds risk. Skipping safety steps turns small hazards into major injuries. The more often workers take shortcuts, the more comfortable they get with risk. They stop seeing the danger. Until it’s too late. A missed PPE check – One forgotten glove leads to a lost finger. A rushed equipment inspection – A worn cable snaps under pressure. Ignoring proper lifting technique – A split-second strain causes years of back pain. Skipping lockout/tagout – A machine restarts with someone still inside. Rushing through confined space protocols – One bad reading, and toxic gases take a life. Shortcuts threaten everyone. They cost companies millions in lost productivity, compensation claims, and lawsuits. A rushed job today can shut down a whole operation tomorrow. And when tragedy strikes, it’s not about money. It’s about lives changed forever. Families devastated. Reputations ruined. Key Takeaways Lorem Ipsum is simply dummy text of the printing and typesetting industry. Lorem Ipsum has been the industry’s standard dummy text ever since the 1500s, when an unknown printer took a galley of type and scrambled it to make a type specimen book. It has survived not only five centuries, but also Lorem Ipsum is simply dummy text of the printing and typesetting industry. Lorem Ipsum has been the industry’s standard dummy text ever since the 1500s, when an unknown printer took a galley of type and scrambled it to make a type specimen book. It has survived not only five centuries, but also Lorem Ipsum is simply dummy text of the printing and typesetting industry. Lorem Ipsum has been the industry’s standard dummy text ever since the 1500s, when an unknown printer took a galley of type and scrambled it to make a type specimen book. It has survived not only five centuries, but also Lorem Ipsum is simply dummy text of the printing and typesetting industry. Lorem Ipsum has been the industry’s standard dummy text ever since the 1500s, when an unknown printer took a galley of type and scrambled it to make a type specimen book. It has survived not only five centuries, but also Why Workers Take Risks Pressure to Perform – Speed over safety. When deadlines loom, safety steps feel like obstacles. Overconfidence – Workers trust experience over protocol. They think they know better—until they don’t. Bad Habits – Cutting corners becomes routine. The more it happens, the more normal it seems. Lack of Accountability – If no one enforces safety, workers assume it doesn’t matter. Peer Influence – If everyone else skips steps, new workers follow suit. Fatigue and Stress – Tired workers make poor decisions. The exhausted brain values speed over caution. The Ripple Effect of One Shortcut A single shortcut spreads. A rushed inspection today leads to faulty equipment tomorrow. A minor slip-up turns into a major incident. One unsafe act signals to others that safety is flexible. It erodes the entire safety culture, bit by bit, until disaster is inevitable. Related read: Do you own a business in the insurance industry? Check out how Artificial Intelligence is transforming the insurance industry. How to Stop the Shortcut Mindset Safety isn’t a box to check. It’s a mindset. A culture. Here’s how to stop the “just this once” mentality before it turns deadly: Slow Down – Safety takes seconds. Recovery takes months. Reinforce that no deadline is worth an injury. Reinforce Training – Keep safety top-of-mind with regular refreshers. Make it stick with real-world examples. Encourage Reporting – If workers see shortcuts happening, they should speak up—without fear of punishment. Hold Everyone Accountable – From the top down, safety is non-negotiable. No exceptions. Reward Safe Behavior – Recognize workers who take the time to do things right. Reinforce that safety matters more than speed. Use Real Consequences – Don’t just warn about risks. Show examples. Videos. Stories. Accidents that could have been prevented. Supervisors Must Lead – Leaders who enforce shortcuts set a dangerous precedent. Safety starts at the top. The Bottom Line A shortcut isn’t just a time-saver. It’s a risk multiplier. One bad decision can cost a life. The safest worker isn’t the fastest—it’s the one who makes it home. Every. Single. Day. Because safety isn’t about slowing work down. It’s about making sure work never stops because of an avoidable tragedy. BIS Social Media Follow BIS Safety Software for industry-leading safety updates, training solutions, and more. Hover over each icon for quick access to follow, share, or explore our other channels. Frequently Asked Questions Have question in mind? We are here to answer. If you don’t see your question here, drop us a line at our contact page. Lorem Ipsum is simply dummy text of the printing and typesetting industry? Lorem ipsum dolor sit amet, consectetur adipiscing elit. Ut elit tellus, luctus nec ullamcorper mattis, pulvinar dapibus leo. Lorem Ipsum is simply dummy text of the printing and typesetting industry? Lorem ipsum dolor sit amet, consectetur adipiscing elit. Ut elit tellus, luctus nec ullamcorper mattis, pulvinar dapibus leo. Lorem Ipsum is simply dummy text of the printing and typesetting industry? Lorem ipsum dolor sit amet, consectetur adipiscing elit. Ut elit tellus, luctus nec ullamcorper mattis, pulvinar dapibus leo. Lorem Ipsum is simply dummy text of the printing and typesetting industry? Lorem ipsum dolor sit amet, consectetur adipiscing elit. Ut elit tellus, luctus nec ullamcorper mattis, pulvinar dapibus
The 5 Most Overlooked Workplace Hazards
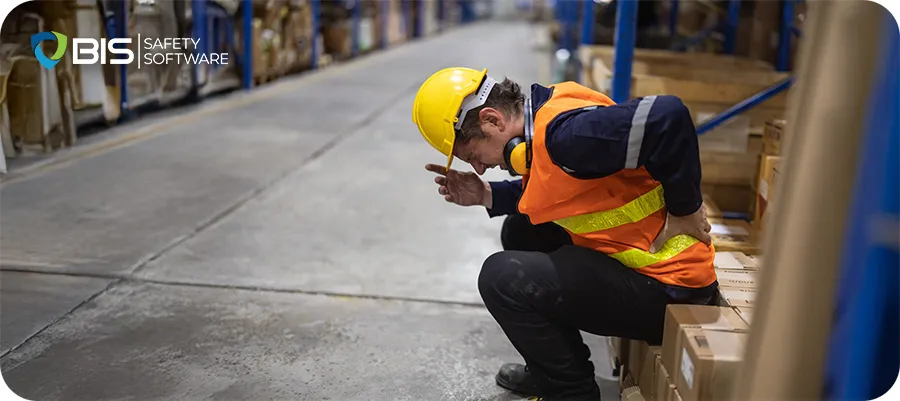
Home The 5 Most Overlooked Workplace Hazards And How to Fix Them Lorem ipsum dolor sit amet, consectetur adipiscing elit. Ut elit tellus, luctus nec ullamcorper mattis, pulvinar dapibus leo. March 7, 2025 By Luke Hillenbrand Workplace safety isn’t just about hard hats and high-visibility vests. Some dangers hide in plain sight. You don’t see them until someone gets hurt. Many risks grow over time, unnoticed. A small ache turns into a disability. A moment’s distraction causes catastrophe. Here are five hazards that often slip by and how to stop them. 1. Poor Ergonomics Sitting all day seems harmless. It’s not. Bad posture and repetitive movements wreck joints and muscles. Office workers, warehouse staff, and factory crews all suffer. Over time, pain turns into lasting damage. Injuries creep in—strained wrists, stiff necks, aching backs. Productivity drops. Workers call in sick. Minor discomfort today becomes a major problem tomorrow. Fix: Adjust chairs, desks, and screens. Teach proper lifting. Offer ergonomic assessments. Small tweaks—like raising a monitor or using anti-fatigue mats—make a big difference. Encourage movement. Stretching and short breaks prevent strain. Rotate tasks to reduce repetitive stress. 2. Mental Health Strain Stress doesn’t leave bruises, but it cripples workers. Burnout and anxiety make mistakes more likely. A distracted worker is a dangerous one. Fatigue slows reflexes. Irritation sparks conflict. Low morale leads to high turnover, more sick days, and poor focus. A stressed worker is an accident waiting to happen. Fix: Foster an open culture. Let employees talk about mental health without fear. Offer support programs. Push for realistic workloads. Breaks aren’t a luxury—they’re a necessity. Flexibility and mentorship help keep teams strong. Train supervisors to spot warning signs. A quick check-in can prevent a breakdown. Key Takeaways Lorem Ipsum is simply dummy text of the printing and typesetting industry. Lorem Ipsum has been the industry’s standard dummy text ever since the 1500s, when an unknown printer took a galley of type and scrambled it to make a type specimen book. It has survived not only five centuries, but also Lorem Ipsum is simply dummy text of the printing and typesetting industry. Lorem Ipsum has been the industry’s standard dummy text ever since the 1500s, when an unknown printer took a galley of type and scrambled it to make a type specimen book. It has survived not only five centuries, but also Lorem Ipsum is simply dummy text of the printing and typesetting industry. Lorem Ipsum has been the industry’s standard dummy text ever since the 1500s, when an unknown printer took a galley of type and scrambled it to make a type specimen book. It has survived not only five centuries, but also Lorem Ipsum is simply dummy text of the printing and typesetting industry. Lorem Ipsum has been the industry’s standard dummy text ever since the 1500s, when an unknown printer took a galley of type and scrambled it to make a type specimen book. It has survived not only five centuries, but also 3. Invisible Toxins Danger isn’t always visible. Dust, mold, and chemical fumes lurk in the air. They creep into lungs, causing long-term harm. Poor ventilation makes things worse. Workers may not realize they’re exposed until it’s too late. Headaches, dizziness, breathing problems—subtle at first, serious over time. Chronic illness follows. Fix: Test air quality often. Use respirators when needed. Maintain ventilation systems. Train workers to spot symptoms early. Better filters and safer handling reduce risks. Label chemicals clearly. Store them safely. Ensure spills get cleaned up fast. 4. Complacency Familiarity dulls caution. When tasks feel routine, workers cut corners. Safety rules become afterthoughts. One skipped step can lead to disaster. The most experienced workers can be the most at risk—they trust themselves too much. Overconfidence kills. Fix: Keep safety fresh. Hold surprise inspections. Reinforce training often. Encourage workers to call out unsafe behavior. Reward attention to detail. Keep everyone engaged and alert. Rotate duties so routines don’t become ruts. Make safety meetings interactive—not just another checkbox. 5. Improper PPE Use Safety gear only works when used right. Loose masks, missing gloves, or fogged-up goggles won’t protect anyone. Some workers resist PPE—it’s uncomfortable, inconvenient, or forgotten. Others assume they don’t need it. A single lapse is enough for injury. Fix: Train workers to use gear in the correct way. Do regular compliance checks. Make sure PPE fits well and is easy to access. Keep training short, direct, and frequent. Show real-life examples of what happens when someone ignores PPE. Make safety personal. Related read: Do you own a business in the insurance industry? Check out how Artificial Intelligence is transforming the insurance industry. Stay Ahead of the Risks Hidden hazards are still hazards. Spot them early. Fix them fast. A safe workplace doesn’t just happen—it takes constant effort. Safety isn’t a one-time meeting. It’s a daily commitment. Keep safety a priority. Stay sharp. Stay safe. A moment of caution saves a lifetime of regret. BIS Social Media Follow BIS Safety Software for industry-leading safety updates, training solutions, and more. Hover over each icon for quick access to follow, share, or explore our other channels. Frequently Asked Questions Have question in mind? We are here to answer. If you don’t see your question here, drop us a line at our contact page. Lorem Ipsum is simply dummy text of the printing and typesetting industry? Lorem ipsum dolor sit amet, consectetur adipiscing elit. Ut elit tellus, luctus nec ullamcorper mattis, pulvinar dapibus leo. Lorem Ipsum is simply dummy text of the printing and typesetting industry? Lorem ipsum dolor sit amet, consectetur adipiscing elit. Ut elit tellus, luctus nec ullamcorper mattis, pulvinar dapibus leo. Lorem Ipsum is simply dummy text of the printing and typesetting industry? Lorem ipsum dolor sit amet, consectetur adipiscing elit. Ut elit tellus, luctus nec ullamcorper mattis, pulvinar dapibus leo. Lorem Ipsum is simply dummy text of the printing and typesetting industry? Lorem ipsum dolor sit amet, consectetur adipiscing elit. Ut elit tellus, luctus nec ullamcorper mattis, pulvinar dapibus leo. Lorem Ipsum is simply
Revolutions in Safety

Home Revolutions in Safety How Dr. Johanna Pagonis is “Womaning Up” Lorem ipsum dolor sit amet, consectetur adipiscing elit. Ut elit tellus, luctus nec ullamcorper mattis, pulvinar dapibus leo. March 5, 2025 By Luke Hillenbrand Dr. Pagonis Puts People and Psychology at the Center. ————————————————————————— “You can have the best systems and equipment. But, if people aren’t empowered to speak up, you’ll always fall short.” Dr. Johanna Pagonis ————————————————————————— That’s the philosophy guiding Dr. Johanna Pagonis, founder of Sinogap Solutions. Dr. Pagonis, an expert in leadership and psychological safety, has redefined how organizations view safety. Her approach is simple but profound; safety starts with people. Their voices, their courage, and their ability to lead from the heart. Falling Into Safety: A Career Reimagined When Dr. Pagonis launched Sinogap Solutions, her focus wasn’t on safety. But a conversation with a former colleague, Christopher Spasoff, changed her perspective. “Christopher is an occupational health and safety lawyer. He told me, ‘What you’re teaching—emotional intelligence, leading with the heart—this is what the safety industry needs,’” Dr. Pagonis recalls. That idea stuck with her. Dr. Pagonis’ early work focused on mental and psychological health, not physical safety. “I can’t tell you how to design an organization for physical safety,” she admits. “But I can tell you how to empower people to use the tools and systems you’ve already put in place.” For Dr. Pagonis, this is the core of the problem. “Checklists and high-tech gear won’t help. If people don’t feel safe challenging the status quo or proposing new ideas, you won’t achieve your safety goals,” she says. Her mission was clear: teach groups to create safe, innovative, and collaborative environments. Her leap into safety wasn’t just about identifying gaps; it was about bridging them. As she consulted with organizations, she found that psychological safety wasn’t a fringe concept. It was a foundation. “It’s not something you tack on,” she says. “It’s woven into every conversation, every decision.” Psychological Safety as the Foundation Dr. Pagonis’ work centers on psychological safety. The idea that people should feel safe to take risks without fear of punishment is a spearhead. “Organizations often focus on the tangible aspects of safety,” Dr. Pagonis explains. “But psychological safety is just as important. Without it, even the best tools and processes will fail.” Dr. Pagonis trains leaders, through Sinogap Solutions, to create safe spaces. Employees should be able to voice concerns and suggest solutions without fearing retaliation. She emphasizes that this isn’t about creating a “bubble-wrapped” workplace. ————————————————————————— “Psychological safety isn’t about avoiding hard conversations. It’s about having the courage to speak up and challenge the system when it’s needed.” Dr. Johanna Pagonis ————————————————————————— Her training programs teach leaders to be vulnerable, build trust, and listen with empathy. “If leaders don’t set the tone, no one else will,” Dr. Pagonis says. “Brené Brown says it best: what a leader does gives permission for others to do the same.” One of her favorite teaching tools is role-playing difficult conversations. “People often freeze when they’re in the moment,” she explains. “Practicing scenarios teaches them to face challenges without shutting down or escalating.” Dr. Pagonis also emphasizes the importance of consistency. “You can’t build trust with one grand gesture,” she says. “It’s the small, daily actions that matter most.” Key Takeaways Lorem Ipsum is simply dummy text of the printing and typesetting industry. Lorem Ipsum has been the industry’s standard dummy text ever since the 1500s, when an unknown printer took a galley of type and scrambled it to make a type specimen book. It has survived not only five centuries, but also Lorem Ipsum is simply dummy text of the printing and typesetting industry. Lorem Ipsum has been the industry’s standard dummy text ever since the 1500s, when an unknown printer took a galley of type and scrambled it to make a type specimen book. It has survived not only five centuries, but also Lorem Ipsum is simply dummy text of the printing and typesetting industry. Lorem Ipsum has been the industry’s standard dummy text ever since the 1500s, when an unknown printer took a galley of type and scrambled it to make a type specimen book. It has survived not only five centuries, but also Lorem Ipsum is simply dummy text of the printing and typesetting industry. Lorem Ipsum has been the industry’s standard dummy text ever since the 1500s, when an unknown printer took a galley of type and scrambled it to make a type specimen book. It has survived not only five centuries, but also Breaking Barriers in Male-Dominated Industries Dr. Pagonis’ work often intersects with male-dominated fields like law enforcement, construction, and transportation. Her course, “Women Up: Ignite the Leader in You,” addresses the unique challenges women face in these environments. “When I started my career, I spent years in male-dominated spaces,” Dr. Pagonis shares. “As a female civilian in law enforcement, I had to earn credibility in ways my male counterparts didn’t.” Those experiences inspired her to create programs that equip women with the skills and confidence to lead. The Women Up course is on its seventh cohort. The program focuses on building confidence, fostering executive presence, and navigating difficult conversations. “One of the biggest challenges women face is confidence,” Dr. Pagonis says. “Whether it’s speaking up in meetings or advocating for themselves, the gap often isn’t in skills but in belief.” One success story stands out. A participant in the inaugural cohort was a senior executive. She was acting in a temporary role while competing for a permanent promotion. The decision-makers passed her over, claiming she was “stressed” and needed “protection.” Dr. Pagonis calls this a classic case of benevolent sexism. “Her male peers were never told they weren’t promoted because someone needed to protect them,” she notes. They denied her opportunities despite her clear qualifications. The program taught the executive to frame her concerns. It also helped her control her emotions in high-stakes talks. “She went back to her boss, asked him to advocate for her,
Crashing the Safety Party

Home Crashing the Safety Party How Allan Moore Disrupts the Status Quo Lorem ipsum dolor sit amet, consectetur adipiscing elit. Ut elit tellus, luctus nec ullamcorper mattis, pulvinar dapibus leo. March 5, 2025 By Luke Hillenbrand “Nobody ever intended to hurt themselves.” Allan Moore’s words don’t leave much room for ambiguity. A safety veteran, speaker, and author, he has spent decades using hard truths to create change. From oil rigs to boardrooms, Moore has built a career not on telling people what to do, but on showing them why it matters. His story proves that leadership is about connection, not authority. This is an industry that’s equal parts risk, reinvention, and resilience. From the Ground to the Helm Moore didn’t set out to become a safety expert. In fact, his career began in Taiwan as a Mandarin interpreter. One day, the global HSE manager decided she was done with international flights and made Moore the health and safety lead. “I told her I had no experience,” Moore says. “She said, ‘You’re the only one who knows how to say the safety words in two languages.’” What started as an improvised appointment became the foundation for Moore’s career. He threw himself into the role, overseeing plants in Taiwan and Shanghai before returning to Canada. Back home, he managed safety plans for major players like Enbridge, Imperial Oil, and Suncor. ————————————————————————— “I’d spend weeks in the field coaching, auditing, and building safety cultures from the ground up.” Allan Moore ————————————————————————— Moore climbed the corporate ladder, eventually becoming a regional manager for Western Canada. But the role lacked the hands-on connection he craved. “I missed being out there,” he admits. So, he pivoted back to field-based work and never looked back. His time abroad shaped how he approached safety in Canada. In Taiwan and Shanghai, he learned that culture plays a significant role in compliance. “You have to adapt,” he explains. “In Taiwan, hierarchy matters. You can’t just tell people to change without respecting their structure.” This adaptability became his trademark—a skill he brought into every boardroom and field office he entered. Key Takeaways Lorem Ipsum is simply dummy text of the printing and typesetting industry. Lorem Ipsum has been the industry’s standard dummy text ever since the 1500s, when an unknown printer took a galley of type and scrambled it to make a type specimen book. It has survived not only five centuries, but also Lorem Ipsum is simply dummy text of the printing and typesetting industry. Lorem Ipsum has been the industry’s standard dummy text ever since the 1500s, when an unknown printer took a galley of type and scrambled it to make a type specimen book. It has survived not only five centuries, but also Lorem Ipsum is simply dummy text of the printing and typesetting industry. Lorem Ipsum has been the industry’s standard dummy text ever since the 1500s, when an unknown printer took a galley of type and scrambled it to make a type specimen book. It has survived not only five centuries, but also Lorem Ipsum is simply dummy text of the printing and typesetting industry. Lorem Ipsum has been the industry’s standard dummy text ever since the 1500s, when an unknown printer took a galley of type and scrambled it to make a type specimen book. It has survived not only five centuries, but also Disrupting Safety Norms Moore’s passion for safety comes from years of seeing what doesn’t work. As a worker, he remembers how the “safety guy” was often met with disdain. “We hated the safety guy,” Moore recalls. “They were condescending. They came in, wagged their fingers, and left us with a lecture. Nobody wanted to deal with that.” When he moved to safety, Moore knew he had to change. He had to disrupt the finger-wagging stereotype. When he became a safety professional, Moore vowed to do things differently. “Nobody sets out to get hurt,” he says. “So, I made a promise: no condescension, no blame, just honest conversations.” He leaned on concepts like emotional bank accounts—a principle he learned from Stephen Covey’s The 7 Habits of Highly Effective People. “Years ago, I read Stephen Covey’s The 7 Habits of Highly Effective People, and it stuck with me,” Moore explains. “Covey talks about emotional bank accounts. Make deposits with positive interactions, like praise for a job well done. Then, you will have the trust to make a withdrawal when needed. It’s crucial, especially in cultures like Taiwan where people can lose face easily.” Moore’s approach emphasizes empathy and connection. “You can’t preach safety from a soapbox,” he says. “You have to walk into the room, listen, and show people you care.” His candid, human-centered communication has made him trusted in the safety industry. He also brought storytelling into his work. Moore realized early on that stories connect better than statistics. “People don’t remember numbers,” he says. “But they’ll remember the time someone got hurt because a shortcut was taken. Stories stick.” Breaking Borders in Safety Culture Moore’s international experience gave him a unique lens on risk. “In Canada, our risk tolerance is low,” Moore says. “In some other countries, it’s very different. I’ve seen welders using cardboard instead of masks. It’s night and day, but our cautious approach here saves lives.” He’s quick to point out the benefits of Canada’s cautious approach. “Our standards save lives. That’s a fact,” he says. But even here, challenges remain. Mergers and acquisitions, for example, often smash together cultures with conflicting priorities. “It takes time to align those expectations,” Moore says. “But the payoff is worth it.” Cultural differences taught Moore to adapt. In Taiwan, safety compliance often involved balancing respect for hierarchy with the need to speak up. Related read: Do you own a business in the insurance industry? Check out how Artificial Intelligence is transforming the insurance industry. ————————————————————————— “You have to find a way to honor the culture while introducing new standards. People watched what I did more than what I said. If
Rescue 7

Home Rescue 7 A BIS Authorized Partner Lorem ipsum dolor sit amet, consectetur adipiscing elit. Ut elit tellus, luctus nec ullamcorper mattis, pulvinar dapibus leo. February 26, 2025 By Luke Hillenbrand A Leader in Workplace First Aid For over two decades, Rescue 7 has been at the forefront of workplace first aid training in Canada. Founded in 1998 by Toronto firefighter John Collie, the company has grown from a home-based operation to a nationally recognized training provider, equipping thousands of employees with the skills and confidence to respond in emergency situations. ————————————————————————— “We want to give people the tools and confidence to help in real-life situations. That’s what we’re here for.” Michele McCabe General Manager ————————————————————————— Tailored Training Across Canada Key Takeaways Lorem Ipsum is simply dummy text of the printing and typesetting industry. Lorem Ipsum has been the industry’s standard dummy text ever since the 1500s, when an unknown printer took a galley of type and scrambled it to make a type specimen book. It has survived not only five centuries, but also Lorem Ipsum is simply dummy text of the printing and typesetting industry. Lorem Ipsum has been the industry’s standard dummy text ever since the 1500s, when an unknown printer took a galley of type and scrambled it to make a type specimen book. It has survived not only five centuries, but also Lorem Ipsum is simply dummy text of the printing and typesetting industry. Lorem Ipsum has been the industry’s standard dummy text ever since the 1500s, when an unknown printer took a galley of type and scrambled it to make a type specimen book. It has survived not only five centuries, but also Lorem Ipsum is simply dummy text of the printing and typesetting industry. Lorem Ipsum has been the industry’s standard dummy text ever since the 1500s, when an unknown printer took a galley of type and scrambled it to make a type specimen book. It has survived not only five centuries, but also Rescue 7 delivers high-quality, industry-specific training using a combination of instructor-led sessions and blended learning models. Their programs are certified nationwide (except in Quebec, which has a separate regulatory framework) and cater to a wide range of industries, from corporate offices to hazardous work environments. Unlike some international training models that allow fully online certification, Canada requires hands-on instruction. Rescue 7’s expert trainers—who are all active or retired first responders—ensure that participants receive real-world, practical experience that prepares them to act in critical situations. As Michele McCabe explains: ————————————————————————— “In the States and other countries, you can do workplace first aid online. But in Canada, you have to actually learn how to do first aid—how to bandage someone, how to do CPR. It’s not just theoretical.” ————————————————————————— Primary List of Services Blended First Aid Training CPR and AED Certification Workplace Emergency Response Planning First Aid Compliance Training Automated External Defibrillator (AED) Solutions Naloxone & Overdose Response Training Rescue 7 combines expert-led instruction with BIS Safety Software’s digital solutions to deliver accessible, industry-leading safety training across Canada. Proud to Partner with Rescue 7 Through their partnership with BIS Safety Software, Rescue 7 enhances workplace first aid training by integrating blended learning solutions with cutting-edge digital tools. The BIS platform enables seamless course management, reporting, and compliance tracking, making it easier for organizations to certify employees in CPR, AED use, and emergency response. This collaboration ensures that businesses across Canada have access to high-quality, accessible, and regulatory-compliant first aid training. Related read: Do you own a business in the insurance industry? Check out how Artificial Intelligence is transforming the insurance industry. Partnership with BIS Safety Software Rescue 7’s partnership with BIS Safety Software began over a decade ago, playing a pivotal role in the adoption of blended first aid training across Canada. The BIS platform has been instrumental in streamlining course management, reporting, and compliance tracking, making it easier for Rescue 7 to manage large-scale training programs. ————————————————————————— “BIS has been with us from the start. Their system is user-friendly, and the customer service has always been fantastic.” Michele McCabe General Manager ————————————————————————— Rescue 7 works with several governing bodies and uses the BIS platform to track training progress, grant access to reports, and ensure full compliance with industry standards. More about Rescue 7 What Sets Rescue 7 Apart? Expert Trainers: Unlike general educators, Rescue 7’s instructors are paramedics, firefighters, nurses, and doctors with hands-on experience in life-saving situations. Industry-Specific Training: Their courses are tailored for various workplaces, ensuring that hydro workers, police officers, security guards, and other professionals receive relevant, scenario-based instruction. Nationwide Reach: With training locations coast to coast, Rescue 7 serves major corporations, government agencies, and regulated industries. Expanding Beyond Training: AEDs & Emergency Beyond first aid education, Rescue 7 is also one of Canada’s largest distributors of Automated External Defibrillators (AEDs). As an exclusive dealer of Stryker Medical’s AED units (HeartSine and CR2 models), they provide training, maintenance, and inspections for life-saving devices in workplaces across the country. In addition, Rescue 7 is expanding its services to include naloxone kit distribution, reinforcing its commitment to emergency medical preparedness. Looking Ahead: The Future of Rescue 7 Rescue 7 continues to drive innovation in first aid training, with plans to: Expand instructor networks into remote and underserved areas. Support standardization efforts with the Canadian Safety Association (CSA) to unify first aid training across all provinces. Explore virtual first aid training if regulatory changes allow for it, leveraging BIS Safety Software for seamless implementation. BIS Social Media Follow BIS Safety Software for industry-leading safety updates, training solutions, and more. Hover over each icon for quick access to follow, share, or explore our other channels. Frequently Asked Questions Have question in mind? We are here to answer. If you don’t see your question here, drop us a line at our contact page. Lorem Ipsum is simply dummy text of the printing and typesetting industry? Lorem ipsum dolor sit amet, consectetur adipiscing elit. Ut elit tellus, luctus nec ullamcorper mattis, pulvinar dapibus leo.